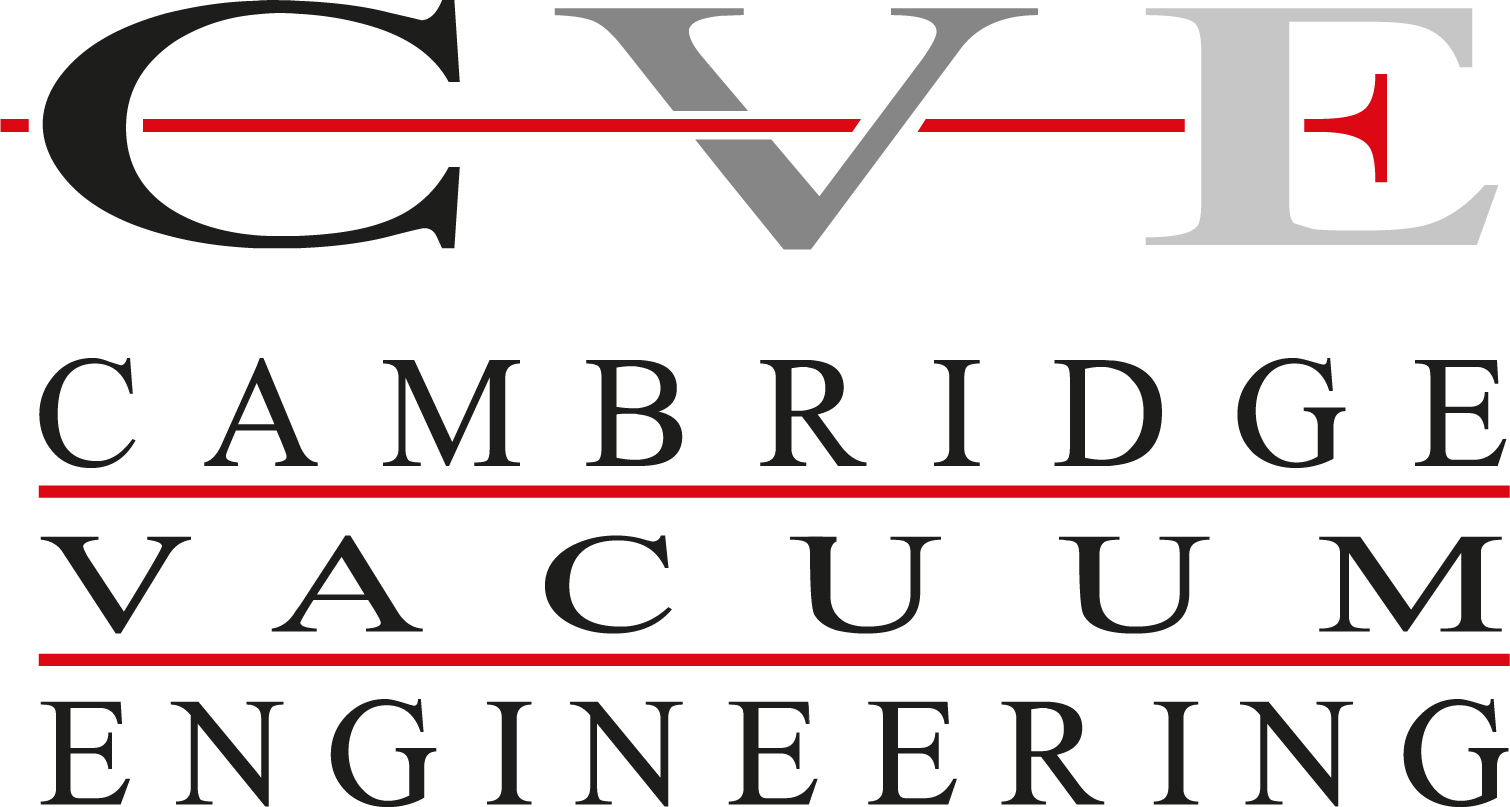
Innovative welding method for large steel structures in offshore wind
Business profile
Welding technology Company headquartered in Cambridgeshire.
60-year history of welding in automotive, aerospace, nuclear, defence and electronics.
Looking to establish electron beam welding technology (Ebflow) to the fabrication of large steel structures in offshore wind – with potential for significant cost and energy savings.
Support recieved
Grant Funding
Solutions for the offshore wind industry
Ebflow electron beam welding offers 20-30x faster welding for large steel structures than conventional welding methods (e.g. slow arc welding).
Up to 20% lower cost than conventional welding.
Up to 90% lower energy use and carbon emissions than conventional welding.
A closer look at Cambridge Vac Engineering support
In 2020, OWGP provided grant funding to accelerate the adoption of Ebflow for offshore wind fabrication in the UK, where it has potential to offer developers and OEMs significant cost and schedule savings for increasingly large offshore wind turbine components.
Impact of the support
Allowed CVE to develop and modify their Ebflow electron beam welding solution for the fabrication of offshore wind foundations and towers.
Paired CVE with Global Energy Group to trial the technology, and integrate Ebflow welding into their planned UK offshore wind tower facility.
Commercial partnership and ongoing support from OWGP is paving the way for accelerated commercial deployment in the UK.
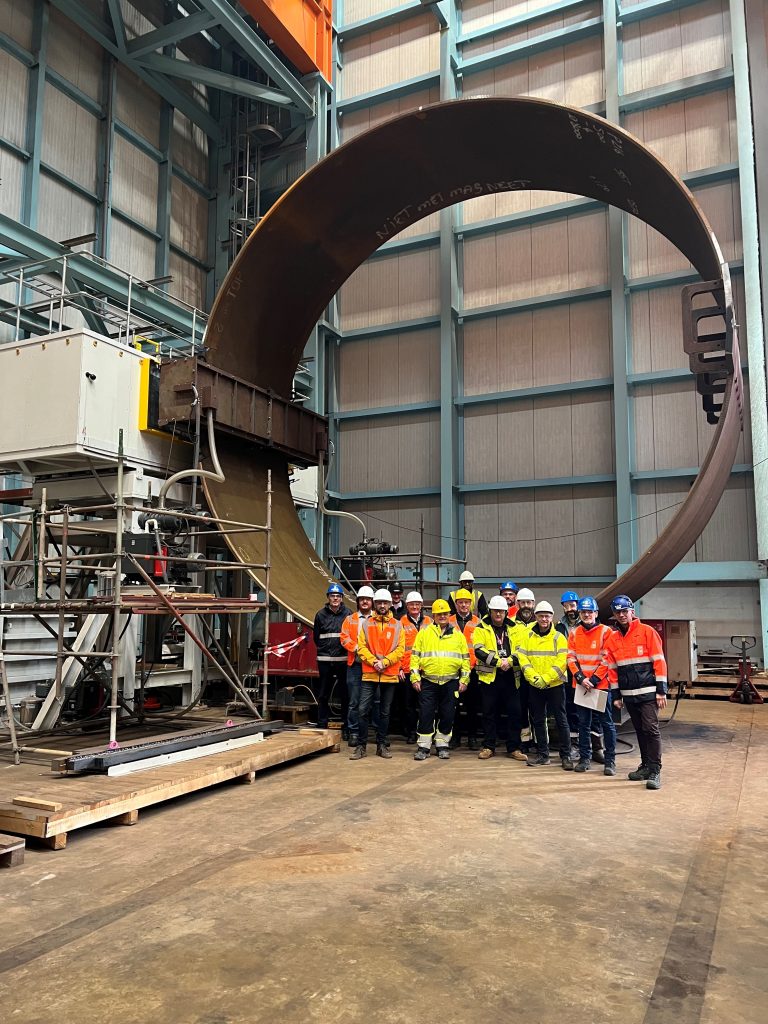
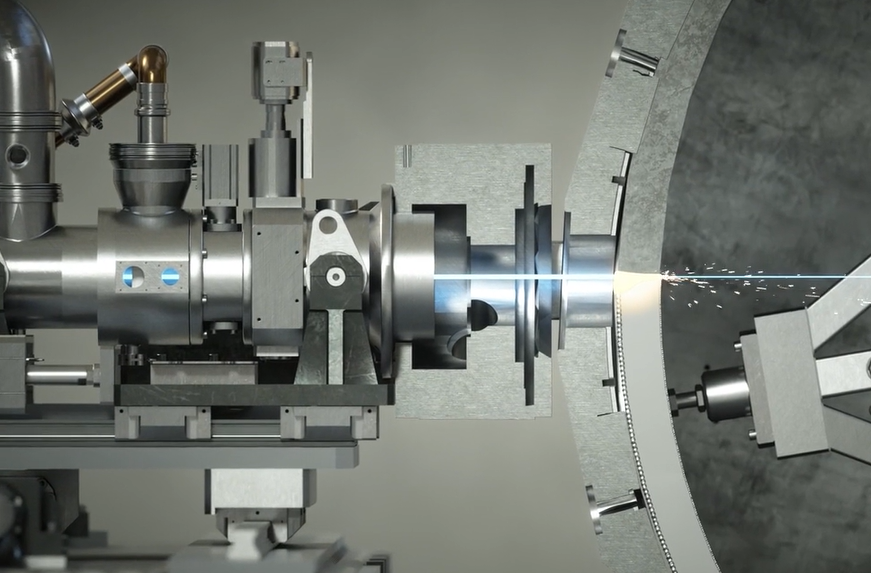
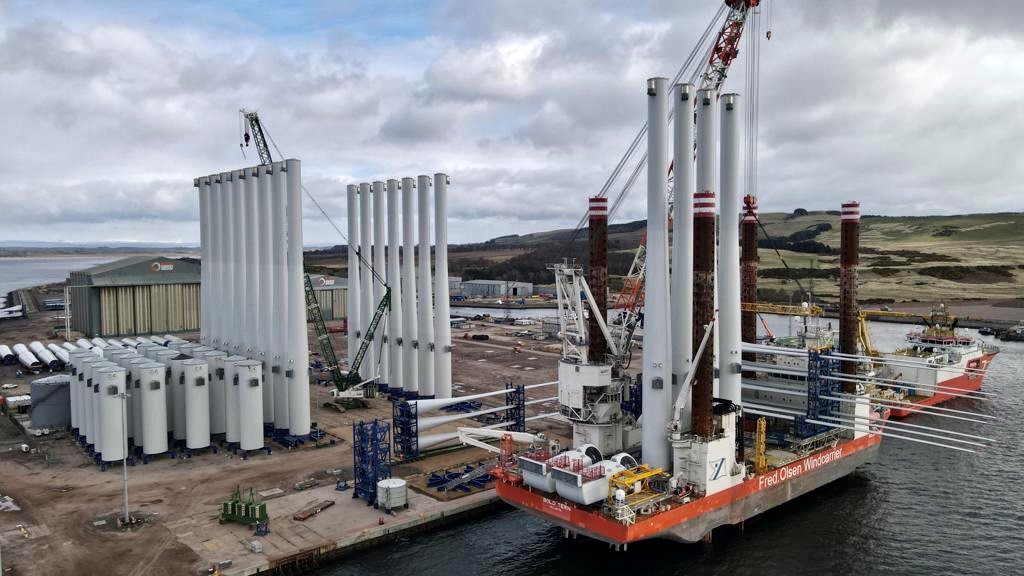
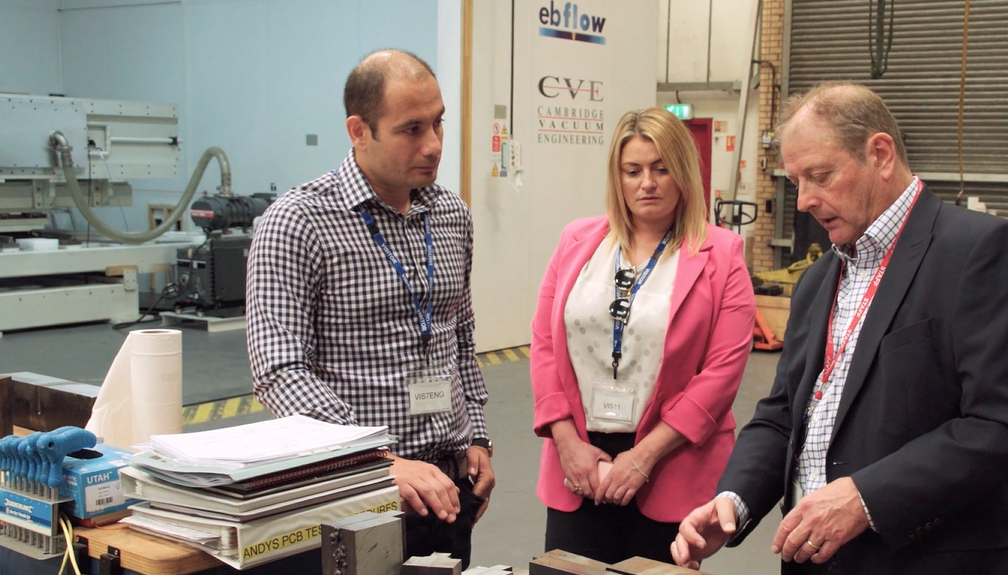
Before
CVE has a 60-year history in the manufacture of welding equipment with numerous applications. They are now looking at the opportunities presented by the energy transition – with key applications for vacuum welding in offshore wind, electric vehicles and semiconductors.
During
CVE had been developing the Ebflow solution for offshore wind for around ten years; the OWGP grant was focussed on accelerating its commercial uptake in the UK market. OWGP remained flexible during the project, adapting to the demands of developing a standardized commercial product – for example, by adapting the initial project scope from circular seam to flat plate welding. With OWGP support, Global Energy Group were selected as industrial partners to help prepare Ebflow for a commercial trial; the aim is to eventually deploy electron beam welding at a planned offshore wind tower manufacturing facility at the Port of Nigg.
After
Global Energy Group (GEG) plan to integrate CVE’s welding technology into its £110m Port of Nigg tower manufacturing facility upon completion, expected 2024. In a separate but complementary project, CVE’s Ebflow technique has been chosen by SSE Renewables, Sif group and TWI to manufacture the world’s first electron beam-welded monopile in an InnovateUK-funded trial. In 2023, this monopile was deployed at Dogger Bank offshore wind farm with the aim to secure industry approval . Alongside this trial of Ebflow at Dogger Bank wind farm, ongoing conversations around industry certification and the continued partnership with OWGP and GEG, CVE are making progress towards commercialisation of a potentially game-changing manufacturing technique for offshore wind, and deploying it in the UK first.
“Ebflow is a disruptive technology that has been in development for 10 years. It is a major breakthrough in thick section, large structure welding and it has applications in a wide range
of industries. The OWGP grant, in conjunction with the RapidWeld project, has the potential to provide a significant step towards the Offshore Wind Sector Deal’s ambition of increasing the UK content of UK offshore wind farms to 60% by 2030. We are excited about the collaboration with GEG, who have demonstrated willingness to adopt new advanced manufacturing processes and are perfectly positioned to integrate this technology into their newly installed manufacturing set-up. Throughout the ongoing programme, we’ve had excellent support from OWGP. They’ve been very flexible in the approach allowing us to modify our program to meet industry requirements”
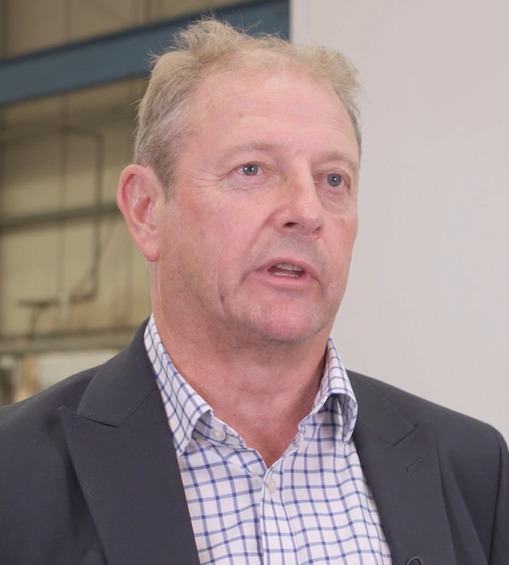